How does a 3D printer work?
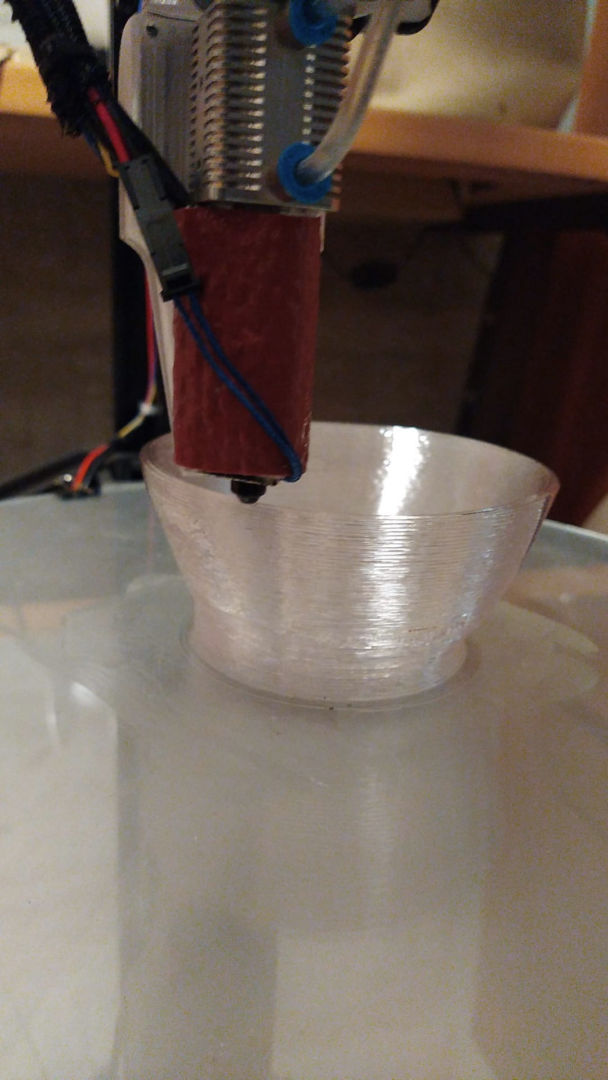
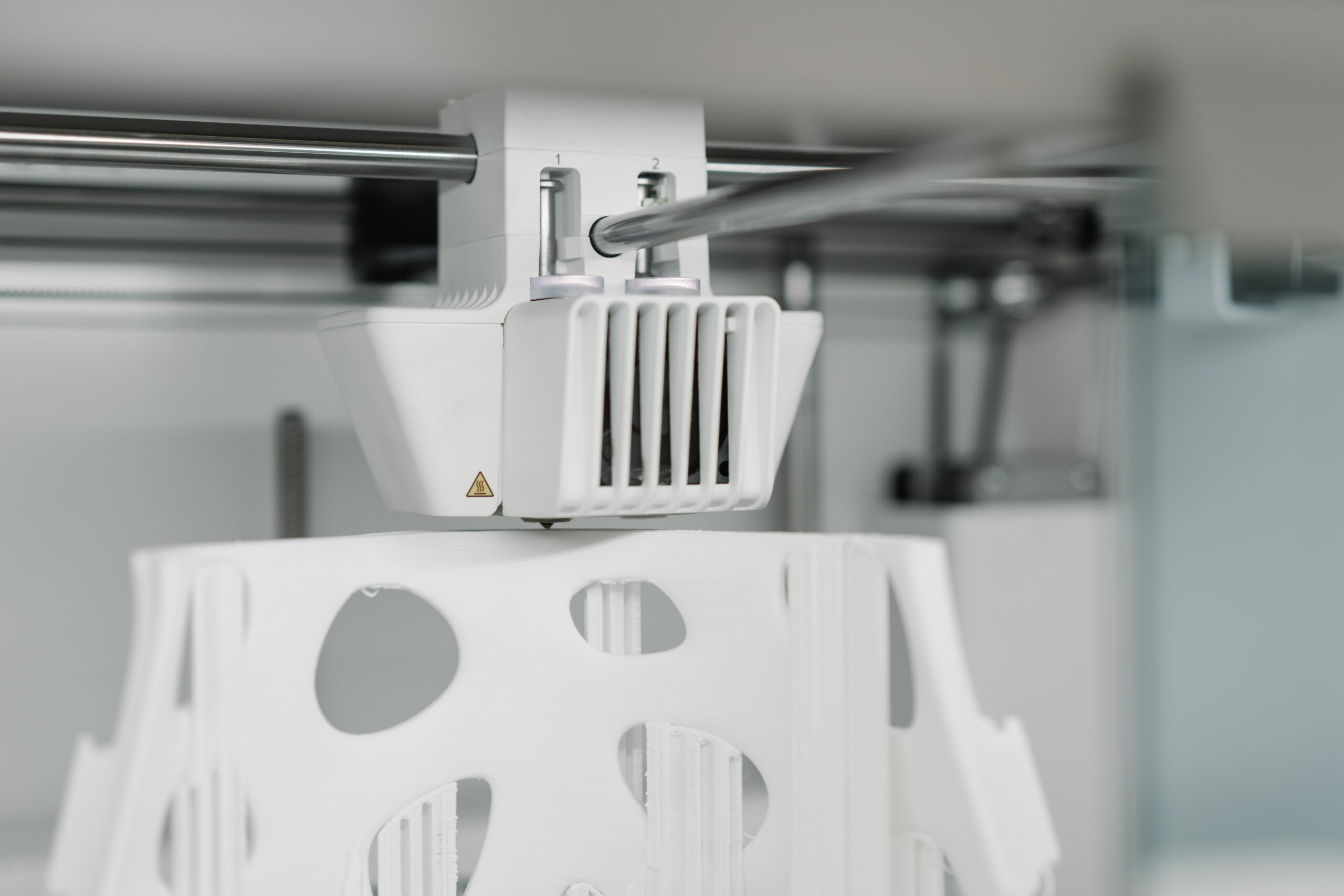
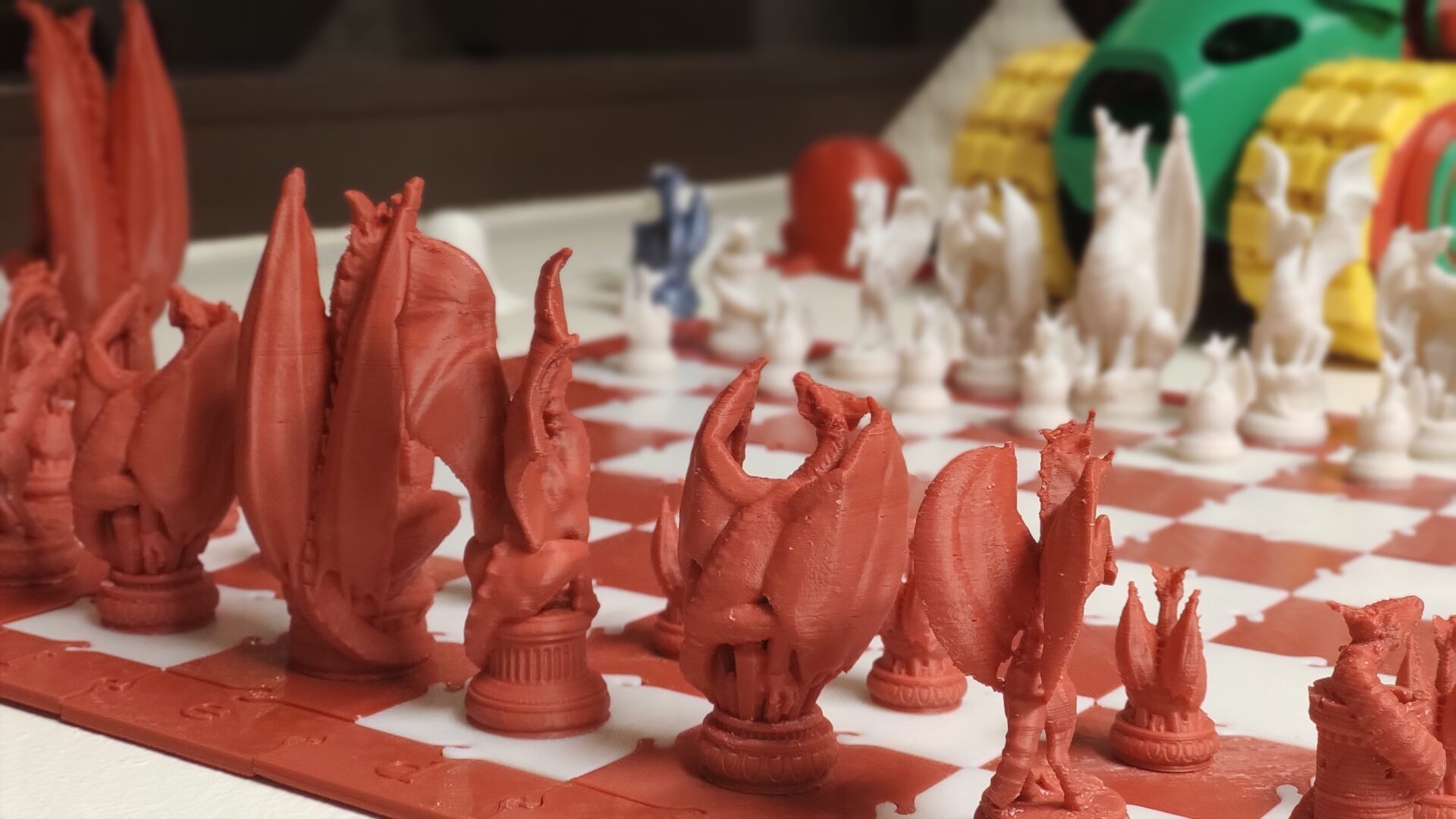
Since their creation in the mid-80s, 3D printers keep on evolving. Multiple technologies have appeared. So how does a 3D printer work?
To understand how a consumer-grade 3D printer works, we’ll focus on one of the most common types availble. Namely, the printers using molten filament, FDM (Fused Deposition Modeling) also sometimes referred as FFF (Fused Filament Fabrication).
- The different parts of a 3D printer
- How a 3D printer works: the different steps
- Other types of printers
The different parts of a 3D printer
The frame
It is a critical part of the printer, as it assures the rigidity of the machine. Built out of steel, sheet metal or aluminum, it has to withstand the various constraints generated by the different elements of the machine. As such, its design is essential to not restrict the precision and speed during printing.
The print head
It is the heart of the printer. By moving in several directions, this is the part that will create your object in 3D. The plastic filament comes in as a solid through the top, is heated and comes out in liquid form out the bottom. It is composed of:
- a filament sensor (optional)
- an extruder that can control the flow of filament to melt. At this stage you will find a gripping wheel and a stepper motor. The latter defines how fast the plastic is pushed through as a means to control flow.
- a hotend, which does the actual printing. It consists of a nozzle that will deposit layers of material on the print surface.
The print bed
Most often composed of an aluminum base with an attached heating element, with a removable print surface above it. The print surface might be glass, metal or composite fibers. The surface can usually be heated. While not mandatory, it guarantees a better adhesion of the molten plastic for the first few layers, depending on the material being printed. You will also find adjustments to properly set the bed square with the print head motion, even if more and more printers include a bed leveling sensor.
The 3 axes on a cartesian printer
The print head position in space is defined by its coordinates along the 3 X, Y and Z axes:
- The X axis defines the width motion (left-right). The print head most often slides on two rails for guidance. It is driven by a stepper motor and has an endstop switch defining the 0 position.
- The Y axis defines the depth motion (front-back). It is most common for the print bed to slide back and forth on two rails. It is driven by a stepper motor and has an endstop switch defining the 0 position.
- The Z axis defines the height motion (up-down). The motion still happens sliding up and down on two axes, but using ball screws attached to stepper motors. For this axis, the endstop switch can either be manually set, or use a probing sensor on the bed plate to define the 0. This allows to define the height between the print head and the print surface.
The electronics board
It’s the board’s responsibility to coordinate all activity on the printer, such as:
- Read and interpret computer code instructions it receives
- Calculate the print head trajectories
- Drive the different printer axis stepper motors
- Modulate the heating elements in the print head and print bed to control temperature
- Manage the LCD screen or SD card onto which the print instructions were stored
The power supply
No power, no printing! It functions the same as the power supply you would find in a desktop PC. It is the power supply who provides all of the power necessary for the printer to function.
The main types of filament
There are several types of filaments, including some specifically engineered towards technical applications. Among the most common, you will find:
- PLA (or PolyLactic Acid): it is one of the most sold plastics because of its ease of use and affordable prices. Primarily derived from corn starch, it’s generally considered safe for food contact and is industrially compostable. It is available in a very wide range of colors and it is used in industrial, medical, and decorative applications.
- PET/PETG (PolyEthylene Terephtalate/PolyEthylene Terephtalate Glycol): These two materials are often used with a certain preference towards PETG. The glycol treatment procures additional rigidity or clarity compared to regular PET. In addition, its strong resistance to chemical reactions, humidity or abrasion make PET a good all-rounder type of material. Add a good recycling lifecycle and it becomes a great choice halfway between the properties of PLA and ABS.
- ABS (or Acrylonitrile Butadene Styrene): along with PLA it is one of the older 3D printing materials in use. It is known for its light weight and impact strength. As with PLA it is found in many applications. The main difference with PLA comes from its tendency to warp (caused by retraction as the plastic cools during the print), which requires a heated bed.
Warping can also happen between layers, which often requires a closed printing chamber to give a uniform cooling rate by avoiding drafts onto the part. ABS is also known to release toxic gases during the heating process, further increasing the need for a closed chamber as it contains the fumes during the print and allowing for proper ventilation of the room the print is happening in.
How a 3D printer works: the different steps
Filament enters the print head
Whether it is PLA, PETG or ABS, the process is the same. Filament, sold in spools, must be routed to correctly enter the print head. On the print head side, the filament sensor lets the print head know that there is material present in addition to acting as an entry point to the filament path.
Movement of the print head (and bed)
The principle of 3D printing is the successive deposition of layers of material to create an object. In cartesian-type printers, generally the print head and print bed coordinate their movements in space. The bed moves along the depth, while the head moves along the width and height of the part.
The electronics board sends the position information (coordinates) to the print head and bed for each layer to print. This is then repeated on each layer until the object is completed.
Filament extrusion
The extruder is the critical piece of the print head, since it is the part responsible for managing the quantity of matter that comes out in a liquid state. There are two main types of extruders:
- Direct drive, where the extruder is built into the print head and it moves around the print volume with it. It increases the entire moving parts weight, and limits print speeds as a result. However, the print quality is increased, especially for flexible filaments.
- Bowden type extruders, where the extruder is before the print head in the filament path, and the extruder can be fixed to a static part of the chassis. The print head becoming lighter it can move at higher speeds while retaining precision, but the amount of pressure the filament is under between the extruder and the hotend is more prone to having issues.
Once the filament has passed through the extruder, it enters the hotend, which has a heating block to melt the material. It also has a heatsink with a fan, to help keep the plastic cool before the melting point. The nozzle is the last stage, before the deposition of material onto the print bed and previous layers.
Other types of printers
- Delta: in this configuration, the print head is controlled by 3 pairs of rods situated in a triangle. I expand on that on the Monster Kossel page.
- Polar: The print surface can turn on itself and move along one particular axis. The 3D effect is obtained by the print head moving vertically.
- Core XY: on a core-XY printer, the print head can move horizontally along both X and Y but not Z. The bed starts just under the nozzle and drops down successively to increase the vertical height. Often coupled with a Bowden extruder, the belt configuration is such that the 2 motors controlling the horizontal move will control motion along a different diagonal. This brings increased speed during moves and thus, during prints.
- Belt based: It is an ideal printer to print smaller parts along X and Y, but really long along Z, as the Z axis is basically infinite.
As you can see, there are many different technologies used for making 3D printers. The material selection is equally diverse with many having specific uses, like resin for example. I am happy to provide advice on how to work with resin, for example. For those questions, and any other 3D printer related question, the easiest way to get answers is to contact me.